Tuning Slow-Responding Control Loops
Once in a while you’ll have to tune a control loop on a process that takes seemingly forever to settle out at its final value. This specifically applies to self-regulating processes where you traditionally have to wait for the process response to fully complete before you can analyze the data for tuning (see: Cohen-Coon Tuning Rules). This becomes exceptionally time consuming if you follow best practices, requiring multiple step tests for tuning the controller. (I recommend doing at least four step tests and then tuning from the average process characteristics).
But, if your process has a very long time constant relative to its dead time (see: Dead Time versus Time Constant), you can take a very nice shortcut to reduce your step-testing time, and that is the core of this blog post. Processes with time constants that are four or more times as long as their dead times have been named pseudo-integrating processes, or near-integrating processes. In the short term, these processes act more like integrating processes than like self-regulating processes. My prime example of a near-integrating process would be gas pressure control in large-volume equipment such as baghouses, furnaces, coke ovens, and distillation columns.
I went through my tuning records and selected a good example of tuning steps that I’ve done on a near-integrating process. It was the control of pressure in a closed-loop system consisting of a coal pulverizer, fan, baghouse, and many meters (yards) of ducting. The system recirculated nitrogen gas to carry pulverized coal from the pulverizer to the baghouse. Make-up nitrogen was continuously added to the system. A vent with a control valve, and a pressure transmitter were provided for pressure control (Figure 1). It was this pressure controller that I tuned.
The first controller output step change that I did on this system revealed that the process responded with a relatively short dead time and a very long time constant (Figure 2). In fact, the system had a deadtime of 21 seconds and a time constant of 166 seconds. You can see from Figure 2 that the pressure had not completely settled out – even seven minutes after doing the first step test. It probably needed another two minutes or so to get to a complete flat line. Doing four step tests on this process would probably have taken 40 minutes or more!
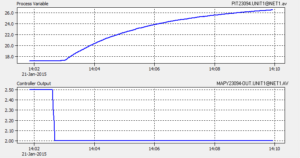
Figure 2. Step response of the system – clearly a very long time constant relative to the short deadtime.
So, I used the shortcut, which is to treat the process as if it is an integrating process. This means do your step tests, data analysis, and tuning as if the process is an integrating process (see Figure 3 for step-test trends). After each controller output change, wait for dead time to run out, wait two additional dead time durations (approximately), and then do your next controller output change. I first heard of this technique from process-control guru Greg McMillan. The data analysis and tuning can then be done as described in this post: Level Controller Tuning.
As you may notice in Figure 3, by treating the process as integrating, I completed eight step tests in half of the time that the one step test took when treating the process as self-regulating. This is a great time saver, and the tuning rules for integrating processes work well on near-integrating processes, although I sometimes increase the integral action (decrease integral time, Ti) to improve the loop’s disturbance response.
By the way, this method applies to more than just processes with very long overall response times. Any self-regulating process may be treated as a near-integrating process, provided that its time constant is equal to or greater than four times its dead time, i.e. tau ≥ 4 x td, regardless of how long or short the process’ overall response time is.
Stay tuned,
Jacques – author of Process Control for Practitioners